Date: 31/10/2023
Read Time: 11 min
Author: Andrew Cox
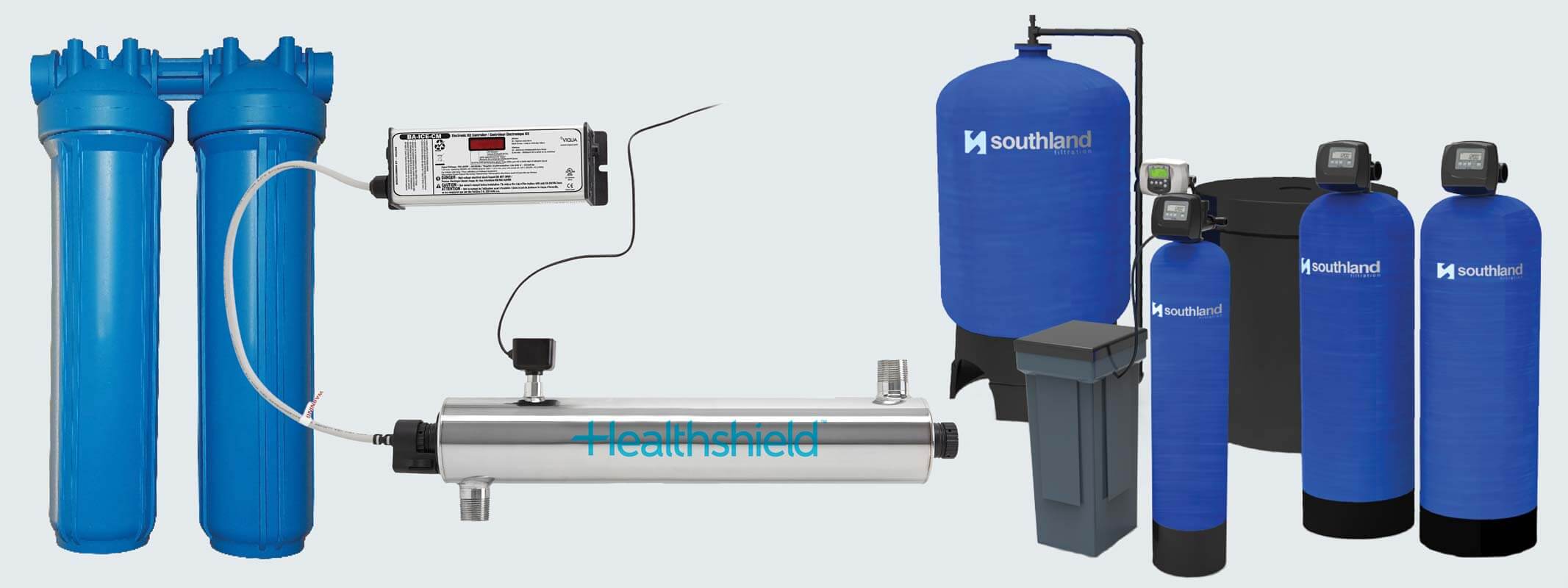
Introduction
Water filtration and purification play a critical role in industrial water use for businesses. Unlike domestic use, industries often require vast quantities of water for various processes, such as manufacturing, cooling, and cleaning. Water sources can contain various contaminants, such as bacteria, viruses, chemicals, and sediments. Ensuring the quality and purity of this water is not only crucial for consumer and patient safety but also for the operational efficiency, environmental responsibility and regulatory compliance of businesses.
Understanding the differences between various water filters is crucial because not all filters are created equal. Different filters employ distinct mechanisms to remove contaminants, and their effectiveness can vary widely. Some filters use physical barriers like mesh or activated carbon to trap particles and chemicals, while others rely on chemical reactions to neutralize harmful substances. By selecting the right filtration system, businesses can optimize their processes, reduce maintenance costs, and minimize their environmental footprint.
Media Filters
How they work
The working of backwashing media filters involves a cyclical process. Water flows through a filter bed containing a filtering medium, such as sand, anthracite, or activated carbon. As the water passes through, the filtering medium captures contaminants, such as sediment, debris, or even microscopic impurities. Over time, this accumulation reduces the filter’s efficiency. Periodically, these filters initiate a backwash cycle. During this phase, the direction of water flow reverses, dislodging and flushing trapped contaminants from the filtering media. The cleansed filter bed is then ready to filter for optimal water quality.
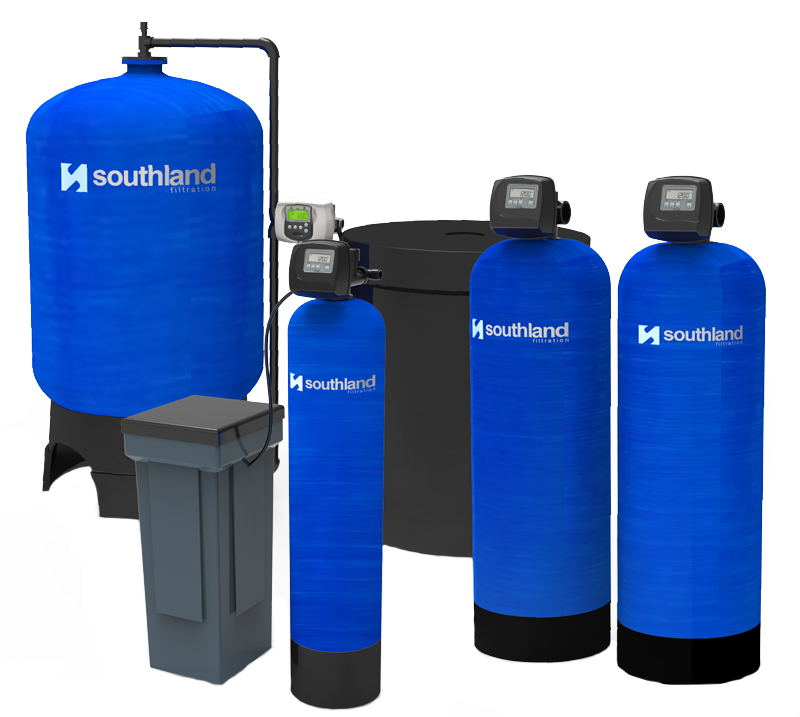
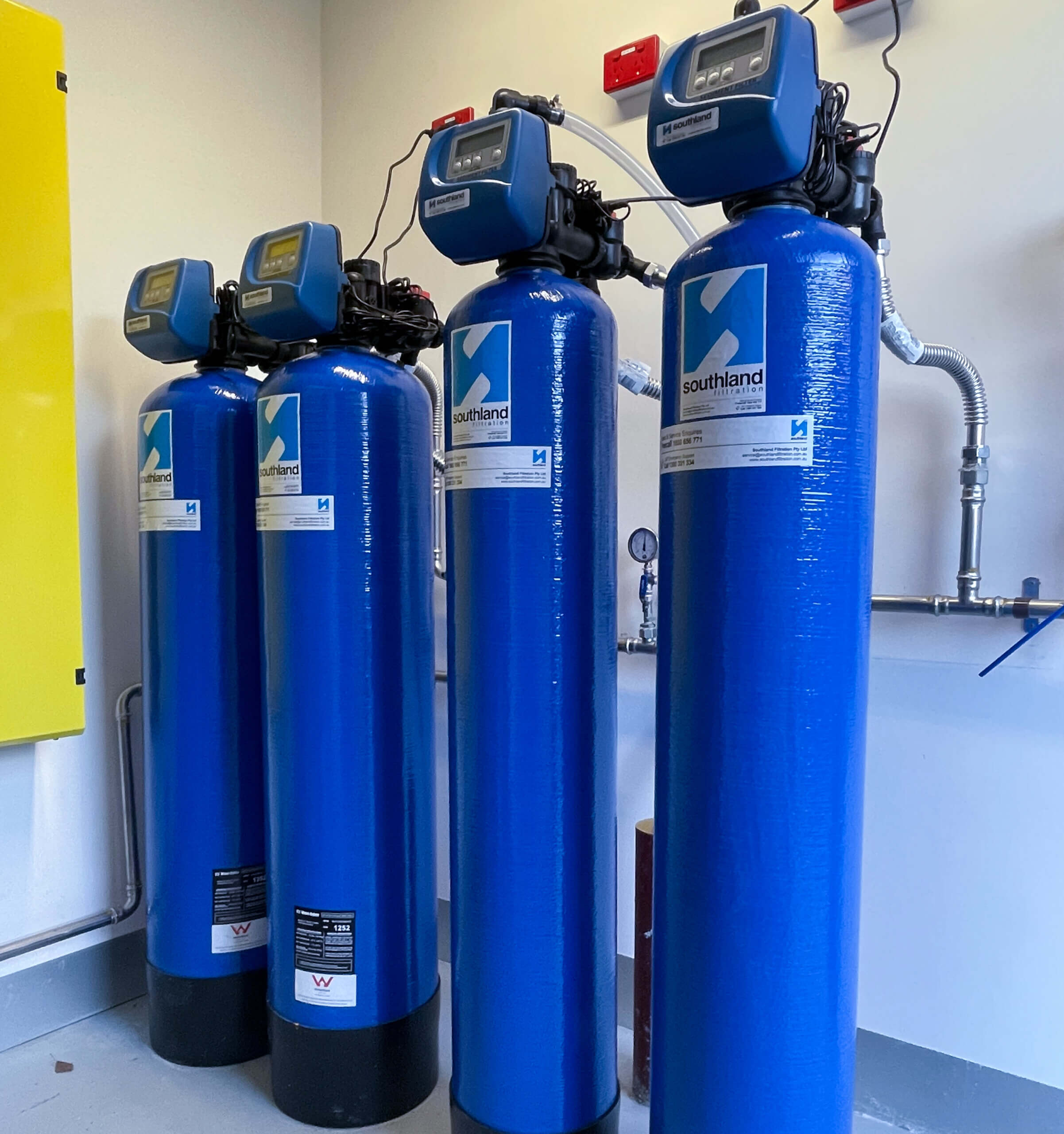
Typical Use Case
Industrial backwash filters find their niche in various sectors and scenarios, proving their worth in demanding industrial environments.
- Manufacturing facilities rely on them to purify process water, ensuring the quality of products and the longevity of equipment.
- Power plants employ these filters to safeguard cooling systems against clogs and damage from debris.
- Wastewater treatment plants use backwash filters to recycle water and reduce environmental impact.
- Mining industry depends on them to extract and treat water from mines, preventing environmental contamination.
- In municipal water treatment plants, they are used to purify drinking water by removing sediments and microorganisms. Industries, such as food and beverage, pharmaceuticals, and electronics, rely on backwash filters to maintain the quality of their products and protect their equipment from clogs and damage caused by contaminants.
UV Disinfection Systems
How they work
UV disinfection systems protect system integrity against microorganisms and pathogens by using ultraviolet light to disinfect water effectively. The damaging effect of UV-C rays on the DNA of microorganisms renders them incapable of reproduction and eliminating the risk of contamination.
As water flows through a UV filter chamber, it is exposed to a high-intensity UV-C light source. This light, at a specific wavelength (typically 254 nanometers), penetrates the cell walls of microorganisms, disrupting their genetic material. The result is that Microorganisms become inactive and unable to reproduce. While the UV-C light works, water passes through the chamber unaltered, with no added chemicals or byproducts. This ensures that the treated water remains safe for hydraulic systems without introducing any potential contaminants.
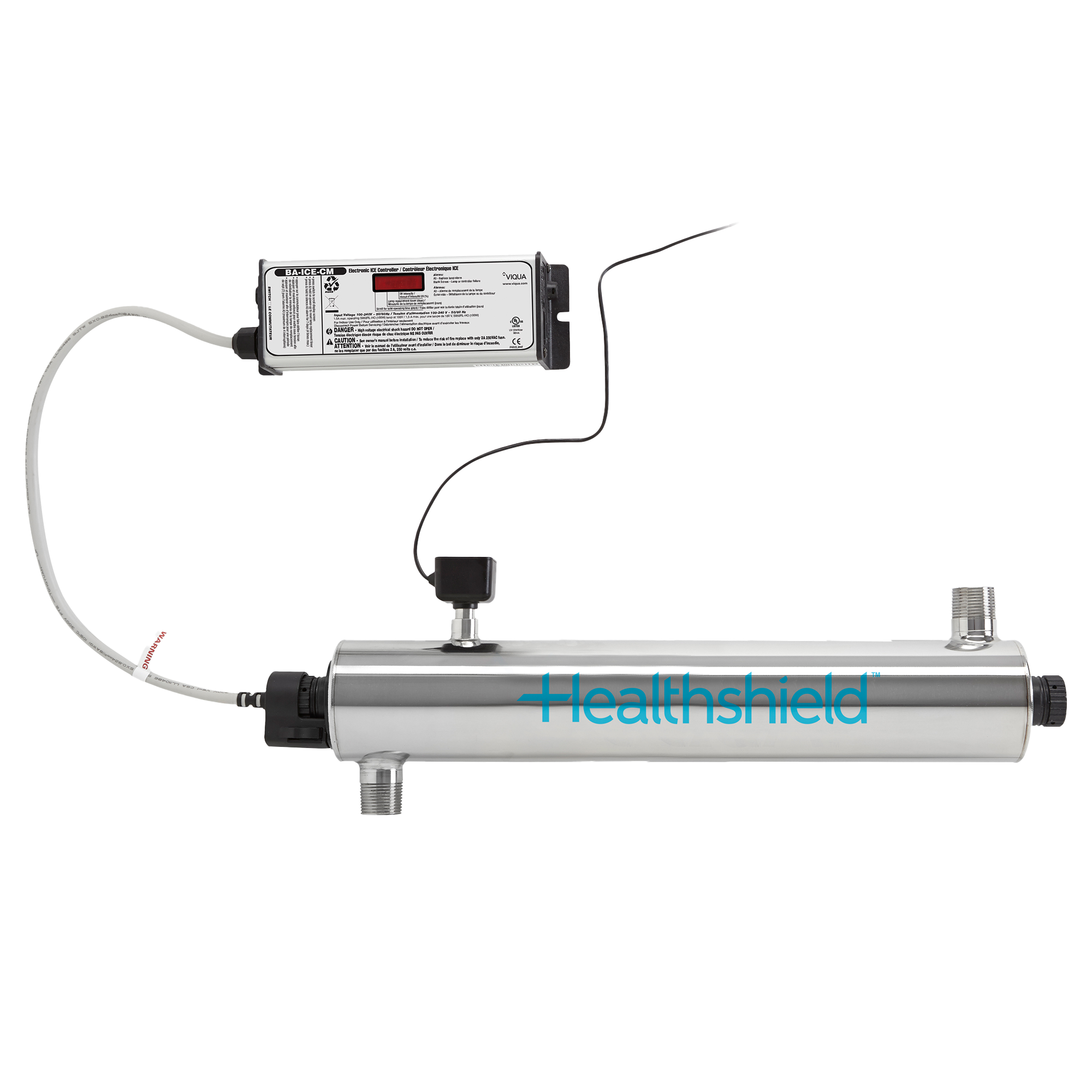
Typical Use Case
Hydraulic engineers employ UV systems in a range of critical scenarios where water quality and sterility are non-negotiable.
- Healthcare for maintaining the sterility of CSSD, renal dialysis, endoscopy suits and laboratories where the purity of water is essential to patient safety and infection control.
- Cooling water systems for power plants, preventing the growth of harmful organisms that can foul heat exchangers and reduce system efficiency.
- In industrial processes, UV filters are deployed to safeguard hydraulic fluids from microbial contamination, ensuring that costly equipment remains in peak condition.
- Municipal water treatment, UV filters are an indispensable component, eliminating the risk of waterborne diseases by neutralizing pathogens
Cartridge Filters
How they work
Cartridge filters efficiently trap and remove contaminants from water sources. These filters operate based on a principle known as depth filtration, where the filter medium captures impurities as water flows through it. The filter medium itself is typically composed of materials like pleated paper, spun polypropylene, or porous ceramic.
As water passes through the filter housing, it encounters the cartridge. Contaminants in the water, whether they are sediment, particles, chemicals, or microorganisms, get entrapped within the filter medium. Clean, filtered water emerges on the other side, free from the potential hazards posed by impurities.
Over time, as the cartridge accumulates contaminants, it can be replaced easily, restoring the filter to its optimal performance. This modular design ensures that water treatment systems continue to deliver clean, safe water without significant downtime or disruptions.
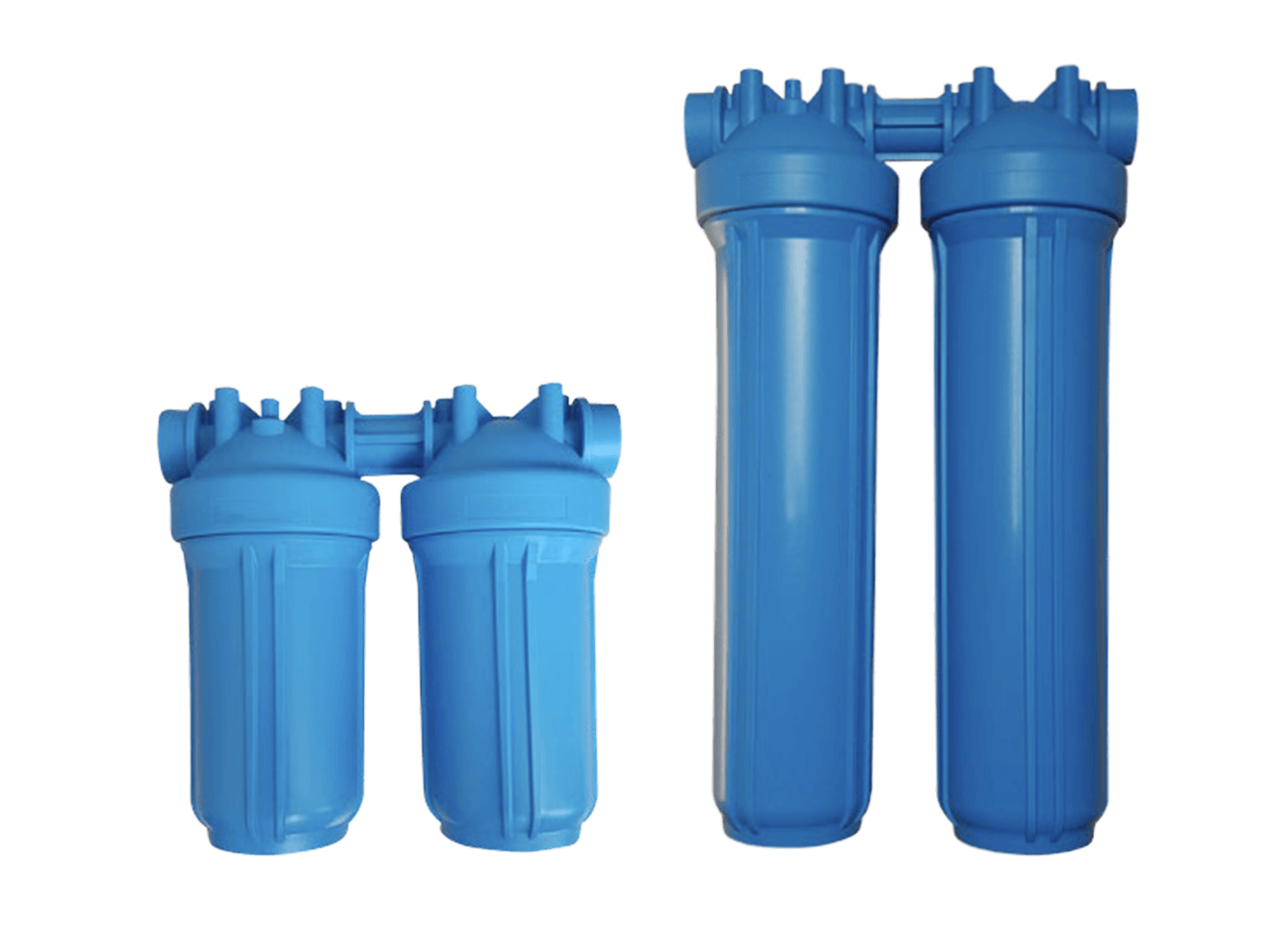
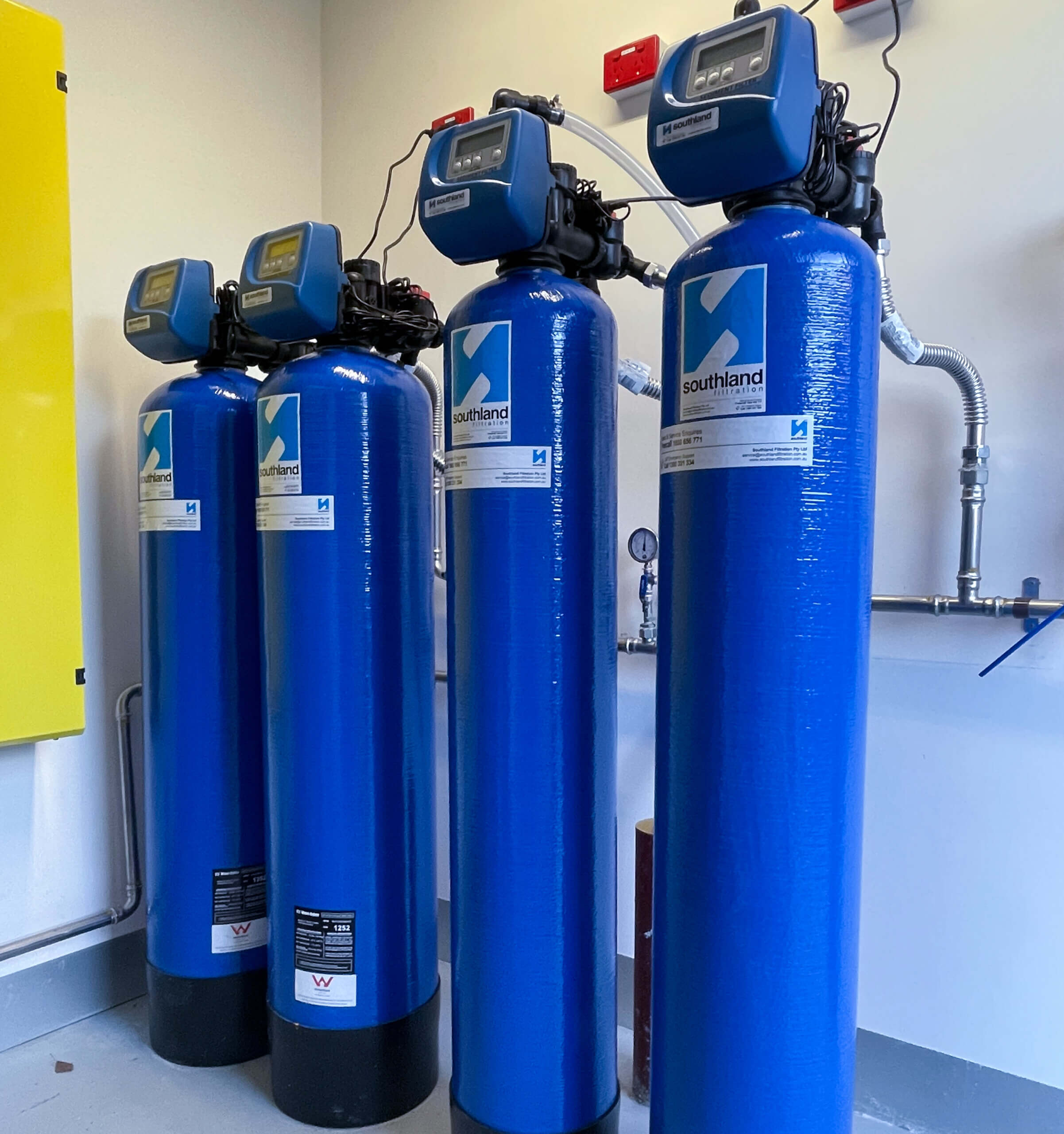
Typical Use Case
Cartridge filters find versatile applications across various water treatment scenarios, where maintaining water quality is paramount. Iindustrial water treatment, cartridge filters play a crucial role in removing suspended solids, chemicals, and microorganisms from process water. These filters are employed to safeguard product quality and equipment integrity in
- Food and beverage production
- Pharmaceutical manufacturing
- Electronics industries
- Municipal water treatment plants to clarify water by capturing particulates and enhancing the efficiency of downstream treatment processes
- Pre-filtration for reverse osmosis systems, protecting delicate membranes from fouling
Efficiency and Contaminant Removal
Environmental Impact and Sustainability
Water wastage in backwash filters
Water wastage can be a concern in backwash filters, especially in the context of water treatment and filtration. During the backwashing process, where the filter media is cleaned by reversing the water flow, a substantial amount of water is often flushed out, carrying away trapped contaminants. While this is a necessary step to maintain filter efficiency, it can result in water loss, which is a critical issue in regions facing water scarcity or where conservation is a priority. To mitigate this, modern filtration systems incorporate strategies to optimize backwash cycles, using sensors and controls to trigger backwashing only when necessary and to minimize the volume of water used. This approach helps strike a balance between the need for clean filters and the imperative to reduce water wastage, contributing to sustainable water treatment practices.
Electrical consumption in UV filters
UV filtration systems rely on powerful UV lamps to emit ultraviolet light for disinfecting water by neutralizing microorganisms. These lamps do consume electricity, and the energy requirement can vary depending on the size and capacity of the UV system. It’s essential to factor in electrical consumption when using UV filters, especially in applications where energy efficiency is crucial. Routine maintenance, such as replacing UV lamps when they reach the end of their lifespan, can help ensure that the system operates efficiently and consumes electricity as intended, ultimately contributing to both effective water treatment and responsible energy use.
Disposal of cartridge filters
Once Cartridge filters reach the end of their lifespan or become saturated with contaminants, they should be handled and disposed of responsibly. Proper disposal involves removing and replacing the used cartridges according to the manufacturer’s guidelines. In many cases, cartridge filters can be disposed of as solid waste or recycled, depending on the materials used in their construction. It’s essential to follow local regulations and guidelines for the disposal of used cartridge filters to minimize their impact on the environment and ensure that they do not contribute to water pollution or other ecological concerns.
Optimising system size and capacity
The key to successful water purification lies in custom sizing the system for your specific needs. Here’s why it’s crucial:
• Off the shelf solutions may not address your specific contaminants or flow rates effectively. Every water treatment application is unique, always source a supplier who will develop a solution specific to your needs.
• You’ll save on time and resourcing costs in the long run as custom-sized systems ensure that water treatment is efficient, and effectively meets the required quality standards.
• You’ll save on overspending on unnecessary features or capacity if you get a system that precisely matches your needs.
To achieve these benefits and get the best value, partner with suppliers who understand the intricacies of water treatment where they can:
• Conduct thorough water quality analysis to identify contaminants and their concentrations
• Evaluate flow rates and system demands to determine the appropriate size and capacity
• Design and supply custom-tailored solutions that address your unique water treatment challenges.
Maintenance and Longevity
The frequency of maintenance for all these filters may vary based on factors such as water quality, usage patterns, and manufacturer recommendations. Adhering to proper maintenance schedules ensures that these filters continue to provide clean and safe water while extending their longevity and preventing potential system issues.
Media Filter
Expected Lifespan
Typically ranges from 10 to 20 years. Varies based on the quality of the filter media, maintenance practices, and the level of contaminants in the water.
Maintenance Requirements & Schedules
Regular maintenance includes monitoring pressure differentials, assessing filter bed condition, and initiating backwash cycles when necessary
UV System
Expected Lifespan
Typically ranging from 9,000 to 12,000 hours of use.
Maintenance Requirements & Schedules
UV filters require periodic checks of the UV lamp’s condition and replacement when it reaches the end of its lifespan. it should be replaced to maintain optimal disinfection performance
Cartridge Filter
Expected Lifespan
Anywhere from a few months to a year before requiring replacement. Depends on filter media, level of contaminants and flow rate
Maintenance Requirements & Schedules
Sediment filters need routine inspection for sediment buildup and cartridge replacement when clogged.
The selection between backwashing media, UV, and cartridge filters is a pivotal decision for hydraulic consultants and engineers tasked with designing efficient and reliable water treatment systems. Each filter type possesses distinct strengths and limitations, making them suitable for different applications. Backwash filters excel in removing sediments and microorganisms, UV filters are highly effective in disinfection, and cartridge filters offer versatility in particle and chemical removal. The decision ultimately hinges on specific project requirements, water quality parameters, and sustainability goals. By carefully evaluating the unique characteristics of each filter type, hydraulic consultants and engineers can tailor their filtration solutions to ensure optimal water quality, system performance, and long-term reliability in diverse hydraulic applications.
Contact Us:
Don’t hesitate to reach out to us today for expert guidance and tailored solutions. Our team of experienced professionals is ready to assist you in evaluating your specific requirements, recommending the best filtration system, and ensuring the long-term success of your water treatment processes. Your solution is just a phone call away. Call 1800 656 771.