Date: 3/9/2024
Read Time: 3 minutes
Author: Dr Surani McCaw, B.E. (Chemical), Ph. D.
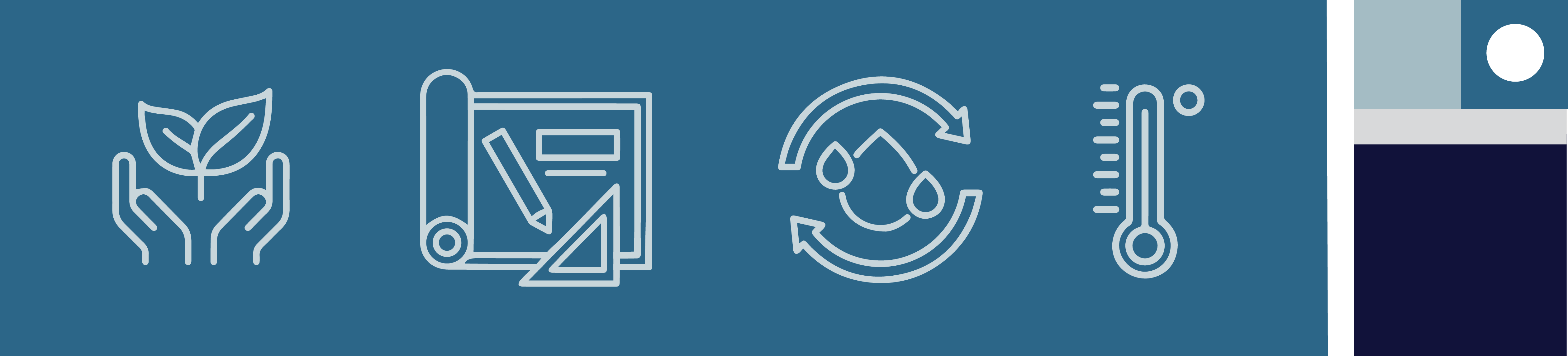
Key points:
- Modern Reverse Osmosis (RO) systems are significantly reducing water wastage through multi-stage membrane configurations and optimised designs, achieving recovery rates of over 75%.
- Advancements in membrane technology and the use of variable speed pumps are lowering energy consumption in RO systems. Additionally, thermal disinfection methods are more efficient than traditional methods.
- Overall, these improvements contribute to a smaller environmental footprint for RO systems, making them a more sustainable and cost-effective choice.
Introduction
Traditionally, RO technology has been associated with significant water and energy wastage. However, recent advancements in RO design are addressing these issues and reducing the overall environmental footprint of RO systems. Key improvements include the following:
Membrane Size and Power Consumption
There is a trend toward using larger 8” x 40” RO membranes to reduce the system footprint in healthcare application. However, larger membranes consume about 18% more power than the traditional 4” x 40” membranes to achieve the same flow rate of 500 L/h. For flow rates exceeding this, power consumption can increase by as much as 270%. To optimise RO system configurations with different membrane sizes, it is essential to use RO process design software, such as ROSA from FILMTEC™ and IMS Design from Hydranautics™, to determine the most efficient design for each application. Additionally, employing variable speed drive (VSD) pumps can further reduce energy consumption.
Water Recovery
When it comes to RO water efficiency, conventional RO systems often waste more than 50% of the water they produce. Modern designs, utilising multistage RO membrane configurations, can achieve over 75% recovery. In these systems, concentrate is directed through additional membrane elements, allowing for more purified water production from the same volume of feed water. This method significantly reduces water wastage and enhances system efficiency. Note that in healthcare application, multistage RO configurations are typically implemented with 4” x 40” membranes for up to 2,000 L/h of RO production, rather than 8” x 40” membranes.
Water Wastage Reduction
Simple yet effective design with integrated feed tank and smarter design in modern RO units minimise water wastage. While traditional RO systems might waste over 25% of water, newer designs can reduce this wastage to between 10% and 25%.
In dialysis applications, where a two-stage RO process is used for redundancy, a common integrated feed water tank helps control feed water quality and facilitates the reuse of majority of the wastewater within the process.
This achievement can be facilitated by demand-based control and water recycling mechanisms. The RO unit can be designed to minimise wastage by monitoring and controlling the water conductivity in the integrated feed water tank.
Thermal Disinfection
Due to the risks associated with chemical disinfectants for patients, chemical-free thermal disinfection has become the accepted standard. This process involves heating water to 80-90°C and maintaining it at this temperature for a specified period to achieve a reduction of more than 99.9% in bacteria.
Although thermal disinfection generally consumes more electricity than chemical methods, smarter process design can reduce the overall electricity consumption of the RO unit. Compared to chemical disinfection, thermal disinfection is often considered a “greener” technology because optimised designs can lead to lower water and power wastage. This makes thermal disinfection a more environmentally friendly option in the long run, despite its higher initial electricity demand.
In applications where RO product water storage tanks are not necessary, such as in dialysis, energy consumption can be reduced by replacing traditional immersion heating of the entire storage tank with rapid inline heaters. This method achieves thermal disinfection in under 3 hours, with the heating element operating for only a fraction of that time. It is more energy-efficient than conventional storage tank heating methods. Proper process control measures are crucial to prevent super heating conditions when using inline heaters.
For dialysis applications, adequately sized inline heaters can achieve an A0 value of 12,000 with a temperature hold time of just 20 minutes. This efficient thermal disinfection process reduces energy consumption and minimises wastage, as shorter disinfection times lead to lower overall energy use.
In Summary
These advancements underscore the continuous improvements in RO technology, with a particular focus on RO water efficiency and sustainability. The shift towards smarter designs aims to balance enhanced performance with reduced environmental impact. Additionally, optimising RO systems often results in significant cost savings that outweigh the initial upfront costs, making them a more economical and environmentally friendly choice in the long term.
Got questions?
We have the answers. Contact Dr Surani McCaw on 1800 656 771 or email Surani.